امروزه تکنولوژی ها با سرعتی باورنکردنی پیشرفت میکنند و تاثیرات آن در صنعت های مختلف قابل مشاهده است. صنعت لوله و اتصالات نیز از این پیشرفت های فناورانه بهرهبرداری کرده است. در این مقاله سعی داریم جدیدترین تکنولوژی های تولید لوله استیل و دو روش تولید این لوله ها را بررسی کنیم.
دسترسی سریع به موارد اصلی
لولههای استیل به عنوان یکی از بهترین و مقاومترین انواع مقاطع فولادی، در صنعت بسیار کاربردی و پراستفاده هستند. این لولهها به دلیل خواص مناسب خود، جایگاه ویژهای در بازار صنعتی دارند. فرآیند تولید لوله استیل نقش بسیار حیاتی در کیفیت و موفقیت محصول دارد. بنابراین، برای بهدست آوردن کیفیت بهتر و بهبود خواص آن در طول زمان، استفاده از تکنولوژیهای جدید و بهروز بسیار اهمیت دارد. در سالهای اخیر، به لطف پیشرفتهای فناورانه و تکنیکهای نوین در فرآیند تولید لوله استیل، بهبود قابل توجهی را شاهد بودهایم. در ادامه، به بررسی دو روش اصلی تولید لوله استیل و تکنولوژیهای مورد استفاده در هریک از آنها میپردازیم.
فرآیند تولید لوله استیل بدون درز
فرآیند تولید لوله استیل بدون درز به معنای خود، به ساختار یکپارچه و بدون درز برای مقاطع لوله اشاره دارد. این روشها میتوانند با استفاده از پیشرفتهای فناوری، بهبود و بهینهسازی کیفیت محصول تولیدی را فراهم کنند. در ادامه، به بررسی انواع روشهای تولید لوله استیل بدون درز و تکنولوژیهای جدید مورد استفاده برای بهبود کیفیت محصول پرداخته خواهد شد.
سوراخکاری دوار (Rotary Piercing)
این روش بهترین و پراستفادهترین روش برای تولید لوله استیل بدون درز است. در این روش، با استفاده از بیلت حرارت داده شده، مندرل حفرهای در لوله را ایجاد میکند. این روش با بهبود طراحی ابزار سوراخکاری و استفاده از سیستمهای خنککننده جدید، بهبود قابل توجهی را در عملکرد و کیفیت لولهها به ارمغان آورده است. همچنین، سوراخکاری دوار با استفاده از سنسورها و سیستمهای مانیتورینگ، به بهبود کنترل پارامترهای مهم فرآیند کمک میکند.
فرآیند سنبه مانیسمان (Mannesmann Plug Mill Process)
این روش نیز یکی از روشهای متداول برای تولید لوله بدون درز است. در این روش، با استفاده از سنبه مخروطی، حفره در بیلت ایجاد میشود و با حرکت سنبه، بیلت تغییر شکل میدهد تا به لوله بدون درز تبدیل شود. بهبود طراحی سنبه مانیسمان و استفاده از آبکاریهای نوین، بهبود قابل توجهی را در عملکرد این روش به ارمغان آورده است. همچنین، استفاده از سیستمهای سرعت بالا و آلیاژهای جدید نیز تحولات مثبتی در این روش ایجاد کرده است.
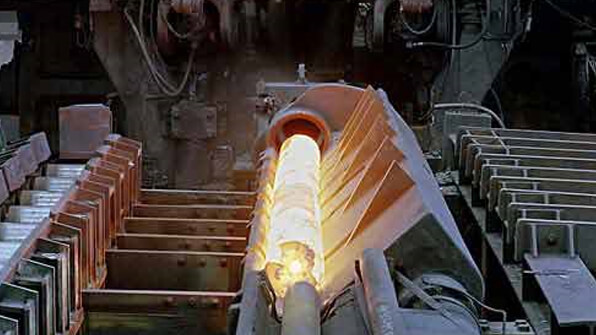
فرآیند سنبه مانیسمان در تولید لوله های بدون درز استیل
اکستروژن (Extrusion)
اکستروژن، یک روش مورد استفاده برای تولید لولههای با اشکال پیچیده و ابعاد کوچکتر است. در این روش، بیلت جامد از طریق قالب فشار داده میشود تا شکل مورد نظر در لوله ایجاد شود. این روش امکان کنترل دقیق تغییرات ابعاد و شکل را فراهم میکند و برای مواردی که نیاز به دقت لوله دارند، مناسب است.
سنبهکاری چند مرحلهای (Multi-Stand Plug Mill)
در این روش، از چندین سنبه که در سری قرار دارند، استفاده میشود. با استفاده از این ساختار دوپشته و قطاری نورد، طول لوله به صورت تدریجی افزایش مییابد تا به شکل نهایی برسد. استفاده از سیستمهای مانیتورینگ آنلاین، به کنترل دقیق پارامترهای مهم فرآیند کمک میکند و عملکرد و کیفیت تولید را بهبود میبخشد.
میز کشش (Push Bench)
این روش برای تولید لوله بدون درز با ابعاد بزرگ مورد استفاده قرار میگیرد. با استفاده از دستگاه میز کشش، بیلت حرارتی به داخل قالب فشار داده میشود و باعث افزایش طول و تولید لوله بدون درز میشود. این روش عموماً در صنایع نفت و گاز استفاده میشود.
استفاده از ابزارهای پیشرفته و طراحیهای نوین در قالبها، بهبود قابل توجهی در کیفیت و عملکرد فرآیندهای تولیدی فراهم کرده است.
فرآیند تولید لوله استیل درزدار
فرآیند تولید لولههای درزدار، در واقع فرآیندی است که در آن دو یا چند قطعه فولادی به منظور تولید لولههای بلند، با یکدیگر جوش داده میشوند. این روش تولید، از روشهای متعددی استفاده میکند که در ادامه به بررسی چهار مورد از این روشها خواهیم پرداخت و درباره تکنولوژیهای استفاده شده برای بهبود آنها توضیح خواهیم داد.
روش جوشکاری فولادی با قوس الکتریکی (Electric Arc Welding)
این روش از قوس الکتریکی برای جوشکاری قطعات فولادی استفاده میکند. در این روش، با ایجاد یک قوس الکتریکی بین قطعات فولادی، جریان الکتریکی از طریق قوس جریان مییابد و باعث انجام فرآیند جوشکاری میشود. این روش بهبود یافته است و با استفاده از تکنولوژیهای پیشرفته و مناسب، کیفیت و عملکرد جوشکاری بهبود یافته است.
روش جوشکاری فولادی با گاز محافظ (Gas Shielded Welding)
در این روش، با استفاده از یک گاز محافظ، اکسیژن هوا از منطقه جوشکاری دور شده و جوش به خوبی انجام میشود. این روش با استفاده از گازهای مختلفی مانند آرگون، دیاکسید کربن و مخلوطهای آنها، بهبود یافته است و عملکرد جوشکاری را بهبود میبخشد.
روش جوشکاری فولادی با جوشکاری الکتروتیگ (Electrogas Welding)
این روش از یک الکترود متحرک و یک جریان الکتریکی قوی برای جوشکاری قطعات فولادی استفاده میکند. در این روش، با استفاده از الکترود متحرک، جوش با کیفیت بالا تولید میشود. این روش نیز با استفاده از تکنولوژیهای پیشرفته و کنترل دقیق، بهبود یافته است و عملکرد جوشکاری را بهبود میبخشد.
جوشکاری مقاومتی الکتریکی (Electric Resistance Welding (ERW))
در روش جوشکاری مقاومتی الکتریکی، از حرارتی که به واسطه جریان الکتریکی در لبه ورق ایجاد میشود، برای ذوب و ایجاد اتصال استفاده میشود. در این روش، دو قطعه فلزی در نزدیکی یکدیگر قرار میگیرند و جریان الکتریکی از آنها عبور میکند. با توجه به مقاومت ماده در برابر جریان الکتریکی، حرارت ایجاد میشود. افزایش حرارت در لبهها، باعث ذوب و ایجاد اتصال جوش میشود. روش جوشکاری مقاومتی الکتریکی عموما برای تولید لولهها، پروفیلها و انواع مقاطع فولادی استفاده میشود.
سیستمهای نظارت و کنترل هوشمند، از جمله تکنولوژیهای جدید در این روش جوشکاری استفاده میشوند. در این سیستمها، از انواع سنسورها، سیستمهای تجزیه داده و هوش مصنوعی برای کنترل پارامترهای کلیدی در حین انجام فرآیند استفاده میشود. این سیستمها بهبودی چشمگیر در کیفیت تولید و به دست آوردن محصولات با بالاترین کیفیت را به ارمغان میآورند. همچنین، استفاده از جوشکاری مقاومتی الکتریکی با استفاده از لیزر یکی از تکنولوژیهای مورد استفاده در این سیستم است. با استفاده از این سیستمها، مزایای هر دو روش جوشکاری بهرهبرداری شده و محصول نهایی با بهترین کیفیت تولید میشود. در این روش، فرآیند جوشکاری به شکل معمول صورت میگیرد، با این تفاوت که ابتدا با استفاده از لیزر، حرارت به قطعه داده میشود و سپس فرآیند به شکل معمول ادامه مییابد.
جوشکاری القایی فرکانس بالا (High-Frequency Induction Welding (HFIW))
در این روش، از گرمایش القایی با فرکانس بالا برای ایجاد اتصال استفاده میشود. در این روش، دو قطعه فلزی در نزدیکی یکدیگر قرار میگیرند و جریان فرکانس بالا به یکی از آنها القا میشود. مشابه روشهای قبل، این جریان باعث ذوب ورق و در نتیجه اتصال آنها به هم میشود.
برای بهبود کیفیت جوشکاری، از تکنولوژی الگوریتم کنترل هوشمند استفاده میشود. در این تکنولوژی، از هوش مصنوعی برای آنالیز و بررسی حجم زیادی از داده و تولید باکیفیت استفاده میشود. اتوماسیون و استفاده از سیستمهای روباتیک نقش مهمی در افزایش بهرهوری سیستم جوشکاری ایفا میکنند. در واقع، این تکنولوژی ترکیبی از سیستمهای اتوماتیک و بازوهای روباتیک برای انجام کارهایی مانند جابهجایی قطعات، تراز کردن قطعات و جوشکاری استفاده میشود. با کاهش دخالت دستی در عملیات و افزایش استفاده از این سیستمها، دقت کار و نتیجه آن بهبود یافته و بهتر خواهد بود.
جوشکاری زیر پودری (Submerged Arc Welding (SAW))
در روش جوشکاری زیر پودری، یک قوس الکتریکی بین یک الکترود یکبار مصرف و قطعه کار ایجاد میشود. این قوس الکتریکی، به صورت یک ساختار پودری مانند، بین دو قطعه جوشکاری اتصال میدهد. استفاده از ساختار پودری در این روش به منظور جلوگیری از آلودگی نقطه جوش استفاده میشود.

فرآیند تولید لوله استیل درزدار – جوشکاری زیر پودری
کیفیت و جنس پودر و الکترود مصرفی در این روش بسیار حائز اهمیت و تعیینکننده است. به همین دلیل، برای بهبود کیفیت جوش و البته محصول تولیدی، تمرکز اصلی باید بر روی بهبود کیفیت و ترکیبات پودر و الکترود مصرفی قرار گیرد. هدف از این تغییرات کاهش زائدههای جوشکاری، بهبود ظاهر جوش و خواص مکانیکی، افزایش مقاومت در برابر شکستگی و زنگزدگی است. در واقع، تکنولوژی در این روش جوشکاری بر اصلاح ترکیبات پودر و الکترود تمرکز دارد تا زبالههای خطرناک و گازهای گلخانهای حداقل شوند. علاوه بر این، استفاده از منابع انرژی تجدیدپذیر و بازیافت ضایعات تولیدی نیز در این روش مورد توجه قرار میگیرد و برای انجام این اقدامات، اقداماتی صورت میگیرد.
جوشکاری لیزری (Laser Welding)
در این روش، از انرژی لیزر برای جوشکاری قطعات فولادی استفاده میشود. انرژی لیزر باعث ذوب شدن قسمتهای موردنظر در قطعات فولادی میشود و با اتصال آنها به هم، لوله درزدار تولید میشود. این روش با استفاده از تکنولوژیهای پیشرفته لیزر و کنترل دقیق انرژی، بهبود یافته است و کیفیت جوشکاری را بهبود میبخشد.